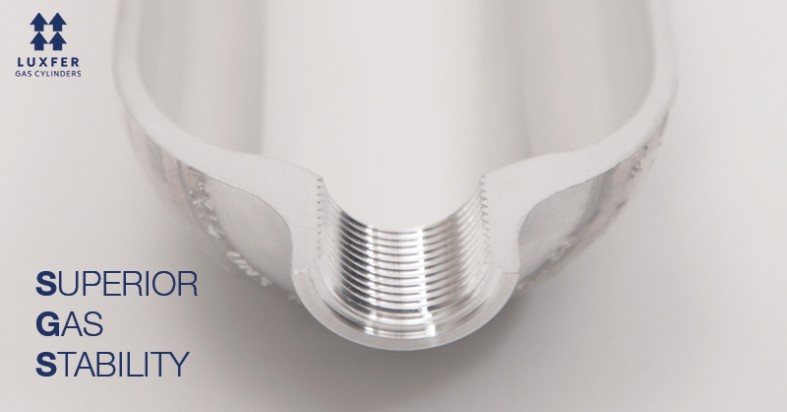
Eric Savonitto, Business Development Manager for Western Europe, has been part of the Luxfer Gas Cylinders team for 15 years, amassing a wealth of knowledge on the components for high quality gas containment. In this blog, Eric looks at the impact on the industry of global shifts, such as supply chain disruption and rising operating costs, and how Luxfer is managing the challenges of the current landscape.
International events such as Brexit, the pandemic, economic uncertainty, rising energy costs and the Ukraine/Russia conflict have led to consequences that few industries have been fully shielded from.
However, Luxfer has remained steadfast in its commitment to quality, performance and safety, as a global supplier of high-pressure gas aluminium and composite cylinders.
Operating across many markets, from medical and healthcare, SCBA and life-support, to alternative fuel systems and more, we are committed to continuous improvement, empowering our team to deliver the very best in cylinder technology to customers, which includes the world’s leading gas companies.
A fast-changing marketplace
The energy crisis sweeping the globe has caused nuclear power developments to surge. With increasing concerns around climate change and air pollution, countries, regions and cities need specialty gases to monitor the atmosphere and as gas detection systems.
There is significant demand for specialty gases from China, as a key player in electronics manufacture, and also in South American countries, such as Mexico and Brazil, as well as Indonesia and India in Asia.
Global economies have experienced seismic shifts since 2020, and industries continue to grapple with the consequences. For Luxfer, we’re well-positioned to support our customers, as a trusted partner in the supply of high quality gas storage solutions that offer performance and long term cost savings.
Ensuring cylinder quality and efficiency
In order to store gases effectively and maintain the efficiency and quality over time, our customers can be confident of the integrity and robustness of a Luxfer cylinder. The internal surface chrematistics, oxide layer and the avoidance of contamination (including moisture) make Luxfer cylinders a ‘go to’ choice for high purity gas products.
So how do we deliver this industry leading internal finish? It is thanks to a powerful combination of factors, including specialist knowledge and expertise, process management and continuous improvement.
Luxfer has the equipment necessary to manufacture to this superior standard, with a highly-controlled process which interrogates every minuscule detail.
For example, we analyse:
- the ingredients in the lubricants we use
- the speed of the press as it ‘punches’ the billet into a cylinder shape
- the purity of the water used for rinsing, which is changed after every batch
- the material of the brushes that touch the internal walls.
Each of these elements will affect the product, and our attention to detail to optimise performance is one of Luxfer’s points of difference.
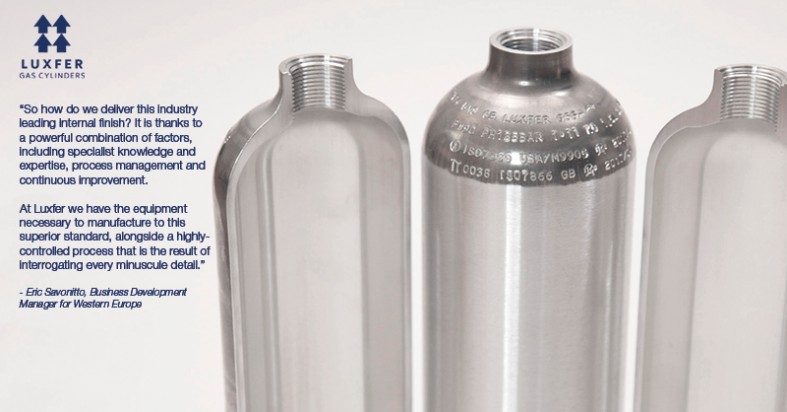
Perfect traceability of every single cylinder
Another important indicator of Luxfer quality is perfect traceability. Every single cylinder produced can be traced from the material we used to make it.
If we identified a cylinder not meeting our standards in internal inspections, we can trace back to the start of the cylinder’s life and isolate each product to a cast and to the exact batch of alloy, and also to the supplier of the materials.
Some gas companies have their own internal test centres and ask Luxfer, as one of their suppliers, to exceed international standards. If our cylinders could not meet these extra requirements, our products would not be as saleable.
We’re confident in the performance of our products and so we welcome this high level of inspection and integrate it into our manufacturing process. It’s crucial that we know we can easily isolate any issues due to our robust traceability.
Luxfer’s ‘secret recipe’
Many gas cylinder manufacturers may claim a ‘secret recipe’, but Luxfer is proud to be at the forefront of developing portable cylinders that can maintain unrivalled gas stability with excellent longevity.
We can achieve this through combining our proprietary metallurgic expertise, with a complex manufacturing process that has been refined over decades.
For most corrosive, aggressive and unstable mixtures, gas companies demand stability for three years. Thanks to our evolutionary processes, Luxfer can offer cylinders with a high-performance internal surface, which is critical to creating the environment that will ensure stability of gases over a long period of time.
It is paramount for the specialty gas industry, where increasingly complex gas mixtures could contain 60 or more components, and need to be certified to purity levels of 99.999%.
There is no room for compromise in such cases, especially when the monetary value of a filled 2 litre cylinder could exceed thousands of dollars. The cylinder must perform so it can protect that customer investment.
Counting costs
The war in Ukraine has affected supply of aluminium from Russia, and this has meant rising prices. However this trend was established, with costs increasing over the past 18 to 24 months. Prices have more than doubled from the end of 2019 to today. The war will create further rarity of aluminium, exacerbating the situation.
Luxfer charges are based on the London Metal Exchange and other indexes, so while no business welcomes price increases, our transparent pricing model means that our customers have full visibility, and they can adjust budgets as needed. Rising costs are an industry-wide challenge, but in terms of value, our customers are aware that with Luxfer they receive premium quality products.
Guaranteeing purity
While gas mixtures were measured in parts per-million (ppm) several years ago, it is now commonplace to measure in parts-per-billion (ppb) and even parts-per-trillion (ppt) – the margins are tiny.
So, although the market is conservative, the demand for cylinders that can guarantee purity and quality is ever more present. Gases are becoming so complex it can take up to ten weeks to inject and mix different layers into the cylinder to ensure the most accurate mixture.
Luxfer has experienced growing demand for ultra-high purity (UHP) gases, and in 2013 we launched our Superior Gas Stability (SGS) aluminum cylinders in the US as a premium option, with a high performance internal surface.
What’s more, we completed a research project examining how we could improve our process to ensure we supply the finest speciality gas products on the market. We’re the only company across the globe to have initiated such a process, to my knowledge.
The only way to measure improvement in quality is via micrographic analysis after manufacture, and it’s difficult to pinpoint with specific measurements the extent to which our cylinders are exceeding expectation of our customers, and the role of our process in that formula. This is why it’s so valuable that we follow a continuous improvement model, with controls after every individual phase of manufacture. It means we offer our specialty gas customers the best of the best.
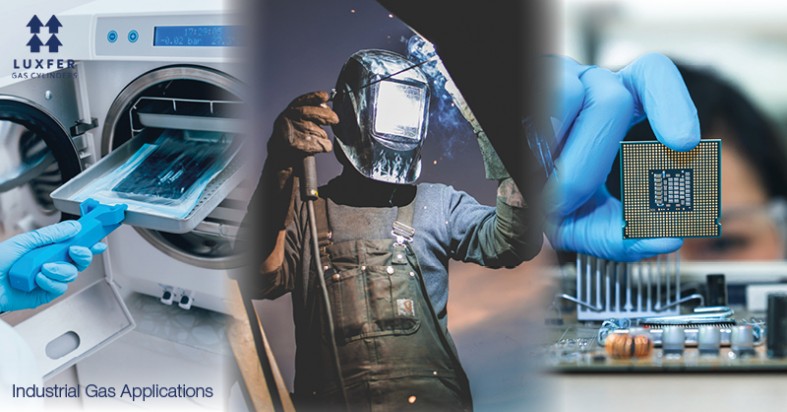
Our metallurgic expertise
Metallurgical innovation – materials science and engineering – is part and parcel of Luxfer philosophy. Our customers who need to store rare, volatile and high-purity gases, such as in the manufacturing of semiconductors and other electronic products, benefit from a superior finish of our Type 1 cylinder, due to our L6X aluminum alloy.
The L6X is part of the 6000 series, and we use the 6061 sub alloy for industrial applications because of its particular composition. Very small percentages of chemicals such as magnesium, calcium or copper are adapted, and make the 6061 sub alloy well suited to this market. Only a handful of companies can supply the quality of materials we need to produce our special recipe.
Formulated in the 1990s to provide optimal durability, fracture toughness and improved tearing resistance, more than 40 million L6X cylinders are now in service in more than 50 countries.