US +1800 764 0366 | Europe & Middle East +44 (0)115 980 3800 | Asia-Pacific: +61 2 7227 5369
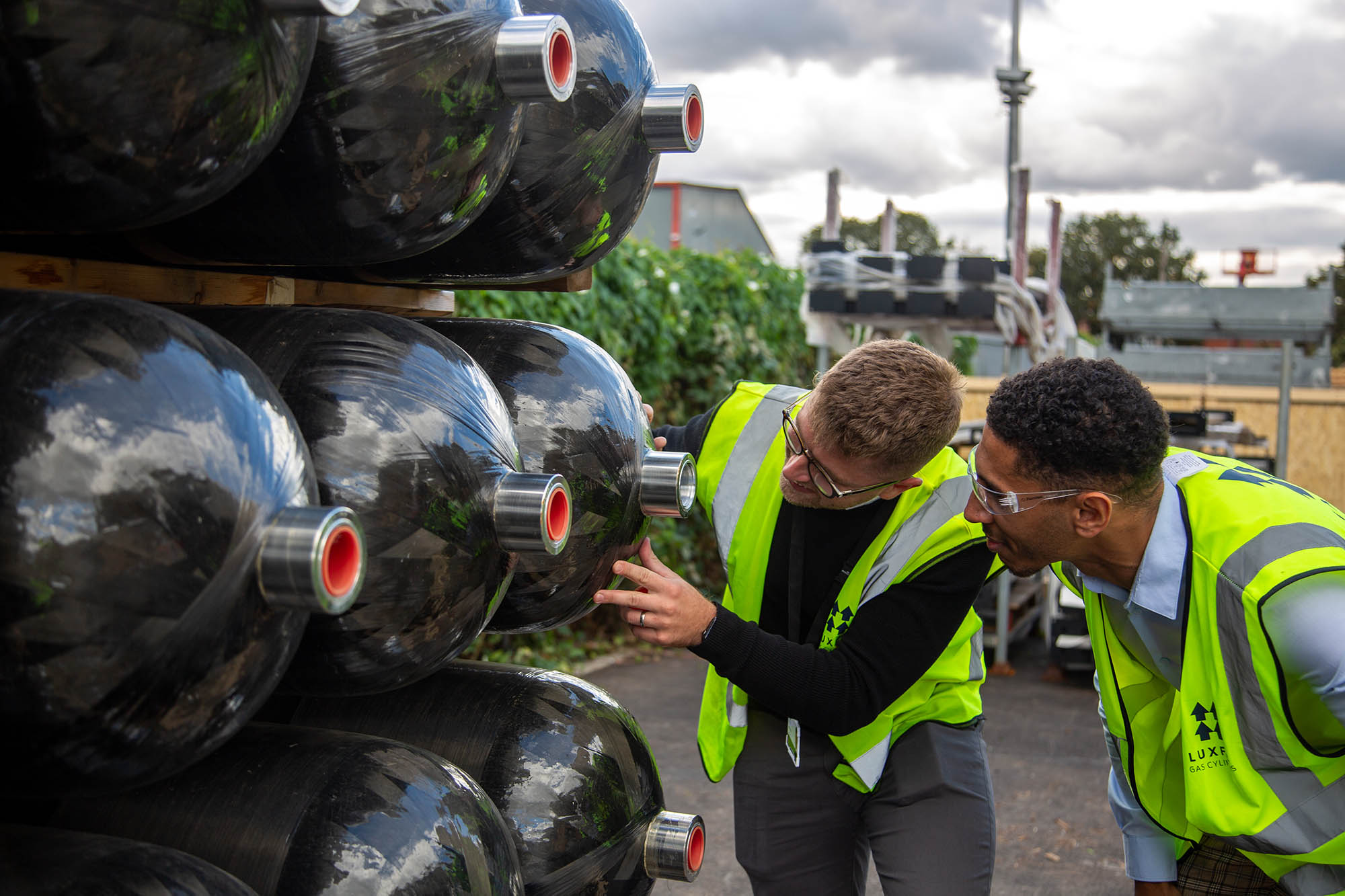
About Luxfer Gas Cylinders
- Customer first
- Integrity
- Accountability
- Innovation
- Development
- Teamwork
We believe that everyone should be able to explore environments with a sense of freedom and a feeling of absolute safety.
We pioneer advances in gas containment that can improve the quality of people’s lives, their health, their well-being and their protection. We achieve this through constant innovation and by working alongside other technology partners to ensure that we maintain our exemplary record for dependability and safety.
It is important to us that our products improve the environment, so we are continuously working towards the reduction of environmentally damaging emissions.
Our Mission
We want to create a safe, clean and energy-efficient world.
Our Vision
At Luxfer Gas Cylinders, we aspire to be the most dynamic cylinder company, providing innovative products in the gas containment industry.
Our Values
Customer First
Integrity
Accountability
Innovation
Personal Development
Teamwork
Our manufacturing locations across the world
We operate as a business unit of Luxfer Group (NYSE:LXFR).
We are headquartered in Riverside, California and we have additional manufacturing facilities in Pomona, California; Nottingham, UK; Calgary, Canada and Shanghai, China.We believe that everyone should be able to explore environments with a sense of freedom and a feeling of absolute safety.
Our Products

What are the different types of cylinders we manufacture?
Type 1 cylinders are manufactured using aluminum billets, through a cold-extrusion process – providing a seamless, complete cylinder.
Type 2 cylinders contain the liner of a Type 1 cylinder, which is then wrapped with carbon fiber around the body of the cylinder to provide lighter weight cylinders, without compromising performance.
Type 3 cylinders are manufactured by fully wrapping a aluminum cylinder liner with carbon fiber. This provides extra strength and support for the cylinder, allowing it to be filled to higher pressures.
Type 4 cylinders contain a plastic liner, that is then wrapped with carbon fiber. Type 4 cylinders have a number of positive qualities, including the adaptability to increase the overall size of the cylinder and the capability be filled to higher pressures.
Association memberships
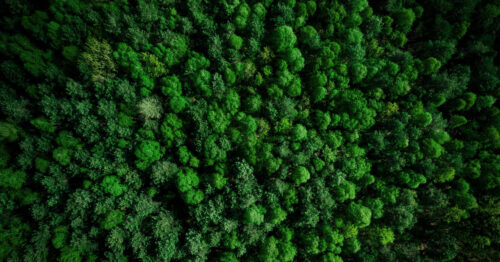
Make an enquiry
Please fill in this form to contact us for sales, support or general enquiries. Thank you.