US +1800 764 0366 | Europe & Middle East +44 (0)115 980 3800 | Asia-Pacific: +61 2 7227 5369
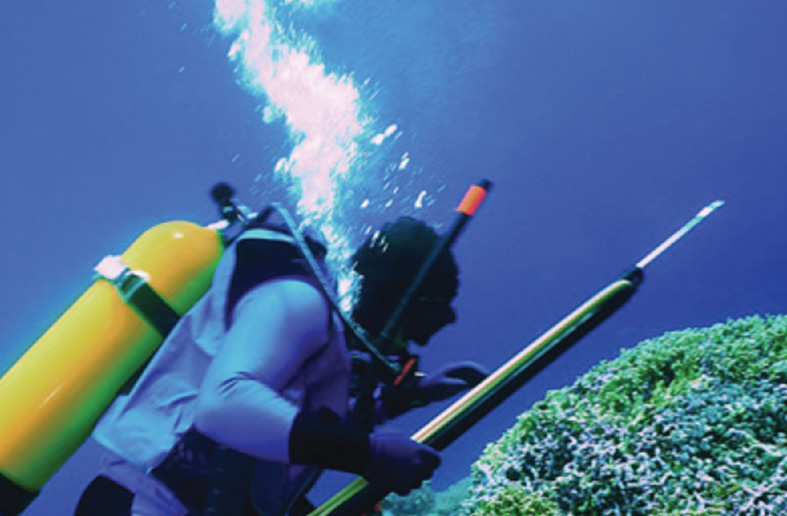
October 28, 1999
DM: How long has PSI been involved with cylinder testing and investigations?BH: I formed PSI, Inc. (initially called Professional Scuba Inspectors) in 1982, following three years of research. I had completed four years as NAUI’s president and was looking for another way to serve the diving community. Our first seminar was conducted in January 1983. We have trained over 10,000 inspectors for military, government, hydrostatic retesting, dive and fire industries in North America, and at numerous international locations. We have 65 instructors in ten countries conducting nearly 200 seminars each year.
What are the main reasons for an aluminium cylinder being condemned and withdrawn from service?
Aluminium cylinders have received a great deal of attention in the USA since an explosion in Riviera Beach, Florida in February 1998. This was widely discussed on the Internet. Before that event, the occasional explosion of either steel or aluminium cylinders was largely ignored by the dive industry. Internal and external corrosion are the main causes of steel cylinders failing inspection or test. Aluminium cylinders fail less often, but when they do the cause is either excessive corrosion, often in the thread area or beneath the boot, or from a crack discovered during a visual inspection.
What does your organisation consider to be the main cause of these problems?
Corrosion damage is usually the fault of the cylinder owner or the fill station. Water, especially salt water, causes metal to corrode. Water lies in contact with the cylinder for days beneath a boot. If air fill stations have poorly maintained filters and water separators, water will be pumped into the cylinder during fills. Sustained load cracking is a defect that appears in some cylinders made from 6351 alloy. In the USA, this alloy was used by Luxfer Gas Cylinders from 1971 through to 1987. All Walter Kidde scuba cylinders were also made from 6351.
Is it hydro testing or visual testing that shows if there is a problem with a cylinder?
Hydro testing does not appear to be the best means to detect a sustained load crack in at-risk cylinders. Most cracks in cylinders are found by visual inspectors. Considering both steel and aluminium, over 90% of the cylinders failed by a hydro retester are failed by visual inspection prior to a pressure test.
Do you have an idea of the percentage of cylinders which fail out of those tested?
If you mean hydrostatic tested cylinders which failed that pressure test, then the number is very small, since most cylinders are failed based upon damage observed by visual inspection. The following example from one of our PSI affiliate instructors who is also a federally licensed hydrostatic retester may help. His retest business is primarily limited to scuba cylinders. He tests about 2000 scuba cylinders each year – these cylinders are visually inspected annually and hydro tested with visual inspection every five years. Of those 2000, he condemns nearly 12% prior to the actual pressure test, due to damage observed that exceeds the allowable limits. Of those that pass the pre-test visual examination and are then pressure tested, he condemns only one or two aluminium cylinders and about ten steel cylinders. This example is consistent with enquiries we have made of other hydrostatic retesters on other occasions.
What can divers do to ensure their aluminium cylinders are safe?
The final responsibility for cylinder safety lies with the cylinder owner. They must realise that an 80 cubic foot capacity cylinder contains more than one million foot/lbs of potential energy, very likely equal to a hand grenade. Divers should clean their cylinders, dry them and store them away from excessive heat, always with some internal pressure. They can demand that the fill station have properly functioning filter/separator systems, fill the cylinder slowly, and not overfill it. Cylinders should be inspected frequently, both internally and externally, by a technician who actually knows what to look for in the way of damage. In North America we found that, regardless of how many years of experience an inspector may have handling cylinders, without formal training they cannot properly assess damage.
Do you have any recommendations for filling/test stations to ensure the safety of their staff and customers ?
I have written several articles and produced a booklet that details safe practices for fill station operations. There are many things fill stations can do. Unfortunately, many dive stores in North America fail to appreciate the power of compressed air. Since most cylinder explosions occur during the filling process, there needs to be a separation of the operator and the cylinder. Separation can be accomplished by either distance or a barrier. Only cylinders that have been inspected by a trained visual inspector and are within the retest period should be accepted for filling.
What staff training procedures are recommended in the USA to ensure that people testing and filling cylinders are competent?
In Canada and the USA there are federal requirements and licensing for hydrostatic retesters. The test procedures are established by law, and enforcement is administered by the Department of Transportation (DOT) or Transport Canada (TC). By law, the retester must take training every three years and be examined by federal enforcement personnel every five years to retain their license. Unfortunately, enforcement is incomplete and there are many hydro retesters who are inadequately trained and certify improperly evaluated cylinders. The retester must conduct a visual inspection as part of the hydro retest, but many don’t know what that entails. The North American dive industry has established its own standard of an annual or more frequent visual inspection. This standard is rather well enforced by dive stores and other air fill stations. There is no legal mandate that the inspectors be trained. However, untrained inspectors have no legal defence if a cylinder they inspected fails explosively. Most dive industry entities – including PADI, NAUI, Luxfer, Catalina, Compair/Mako, most dive stores and several court jurisdictions – accept the PSI training protocol as the industry standard.
What is the number one thing that divers do to affect the structural strength of their steel or aluminium cylinders?
Cylinder owners are probably most guilty of not regularly removing and cleaning the cylinder beneath the boot; and, for salt water divers, not washing and drying the valve/cylinder interface.
What are your recommendations to divers for maintaining their cylinders?
Cylinder owners should insist that a trained visual inspector inspect both the interior and exterior of the cylinder at least annually. In North America we have to recommend that a visual inspector look into the cylinder after the hydro retest to ensure no water or other foreign material has been left inside. Store the cylinder in a dry, cool location with some pressure. Secure the cylinder during transport. Don’t drop the cylinder or allow it to bang against hard objects. If corrosion is noted, clean it away, assess the damage against allowable limits and protect the area from future deterioration.
Does storing a full cylinder for long periods – several weeks or months – have a detrimental effect on its structural strength?
There are several considerations when making this decision. In a clean dry cylinder, clean dry air will store quite nicely for long periods, certainly a year or more. Poorly filtered air containing various hydrocarbons or other contaminants could deteriorate in quality over weeks or months. The cylinder itself is designed for a sustained pressure load during its entire life. If moisture is left in the cylinder, then the increased oxygen in a full cylinder will contribute to more rapid corrosion that in turn could weaken the cylinder dramatically over a matter of months.
More importantly, internal corrosion activity will reduce the oxygen content of the air. In the USA we have two examples of oxygen depletion in steel cylinders (corrosion is more rapid in steel). Following three months of storage, a corroded cylinder contained only 15% oxygen, a near-deadly deficiency. Analysis of a dead diver’s air supply in a heavily corroded steel cylinder revealed a deadly 6% oxygen content. The University of Rhode Island’s study of cylinder internal corrosion reveals that under equal conditions of moisture in cylinders, aluminium cylinders fare much better, so air stored in aluminium cylinders may retain its quality longer.
There is one additional consideration for aluminium cylinders. Because of its low tolerance for heat, and where there is potential for the aluminium cylinder to be involved in a fire, there is merit in storing the cylinder either full or nearly empty (about 20 psig). A 3000 psig aluminium cylinder containing less than about 1500 psig is at risk of exploding in a fire. The metal will lose its strength before the heat causes a rise in internal pressure sufficient to activate the pressure relief device (burst disc).
Do you have any comment on the effect of hydrotesting on the material of aluminium cylinders?
I am not an expert in metallurgy, so can say very little about material integrity. However, there are specialists who believe that the hydro test procedure may not adequately test aluminium cylinders. The manufacturers cycle many test cylinders to hydro test pressure thousands of times with no apparent damage. I have not heard any expert suggest that the hydro test causes damage to the cylinder.
In New Zealand and Australia, cylinders are currently tested every two years, and this may change to every year. In the USA, it is currently every five years and may change to every ten years! What are your thoughts on the wide difference in the period over which cylinders must be hydro-tested?
The hydro test alone is not a very good assessment of a cylinder’s condition. Cylinders with obvious cracks and pinholes have passed hydro retest. US rules for retest were written more than 50 years ago, when cylinders were used very differently to how they are used by divers today. Experience in the USA shows that a five year interval seems to work for most gas industry cylinders. I can’t speak about the logic used by the rulemakers in New Zealand and Australia. Whether the retest is one year, two years, or five years is irrelevant for scuba cylinders unless a technical visual inspection is part of the test. Remember, 90% of the cylinders failed by a retester fail the visual inspection, not the pressure test.
In a test conducted by the University of Rhode Island in 1971, a steel cylinder with a small amount of salt water inside was damaged in 100 days to a point of imminent explosion. If I were only given a choice of my cylinder being either hydro retested by one of our less diligent retesters or by a PSI trained visual inspector, I would take a frequent visual inspection and skip the hydro test. There is a proposal before DOT to eliminate hydro retest and replace it with an ultrasound examination at ten year intervals. The vast majority of gas industry users oppose this dramatic change. Ultrasound cannot test for heat damage, the impact of continual overpressurisation, or a number of other forms of damage. Because of the outcry from the dive industry and others, DOT has delayed its decision on this matter. Scuba cylinders cannot possibly remain in service for ten years without a formal examination. Should this rule pass, the frequency of cylinder explosions will increase rapidly.
Do you think aluminium cylinders should have a finite life, then be removed from service?
I have followed closely the issue of sustained load cracking of aluminium cylinders since 1985. As yet, I have not found a correlation between age and the formation of a crack. We do see more cracked cylinders now than we saw ten years ago. That probably means that we now have more people looking, and we have better tools such as the Visual Plus apparatus to conduct the assessment. Some of the cracked cylinders were made in the 1980s, while many thousands from the 1970s remain in service.
Since the cracks propagate slowly over several years, technical visual inspection of the suspect area at least annually should identify defective cylinders. Our records show less than ten aluminium scuba cylinders exploded in North America and several international locations, including Australia, that were most likely caused by sustained load cracking. Statistically, that is a very small number (several million were made), although tragic for those persons injured.
We know some of those cracks should have been found by the visual inspectors who last looked at the cylinder. Unfortunately they were not properly trained. PSI does not have information that would cause us to urge a condemnation of scuba cylinders over a certain age. We believe that no cylinder owner should imagine that his cylinder must last forever. It could last a lifetime, or as little as a few months. It all depends on its treatment while in service. Scuba cylinders are very well made and pass through a variety of rigorous tests both by the manufacturer and by third party examiners. Almost without exception, those that have exploded would have been removed from service by trained inspectors well before the failure, if the opportunity to inspect them had been there. This suggests that the opportunity for technical visual inspections should exist and be available to all cylinder owners. The cylinder owners then must be willing to have their cylinders condemned when damage beyond allowable limits is found.
Thanks, Bill, for your time in providing our readers with this invaluable information. You have brough up some important points that all divers and cylinder owners should be aware of.